I got an email from a customer the other day who wondered if there wasn’t some way to make G-Wizard more focused to the needs of manual machinists. He felt that it was overly “CNC specific”, and wanted some sort of “CNC versus Manual” switch to make it easier. I need to cogitate more on the idea of a switch, but it is certainly true that if you start dialing up modern tooling in G-Wizard and cutting softer materials, you will end up with feeds and speeds that are impossible–the manual machinist just can’t crank the handwheel fast enough.
Let’s back up just for a second and realize a key thing:
KB 360 Pistons for use in Chrysler Dodge Plymouth Mopar 360 Engines. Stroke These pistons are for use with a 3.580 inch stock stroke Chrysler 360 crank, OEM or aftermarket; Connecting Rod Length 6.123 inch; Wrist Pin Size 0.9842 inch diameter; Ring grooves are 5/64 5/64 3/16; CH Compression Height This is the measurement from the centerline of the piston pin bore to the top flat part of the.
- PCR, RT-PCR, qPCR, qRT-PCR PCR Enzymes PCR SuperMixes Direct PCR RT-PCR qPCR and qRT-PCR SuperMixes; Restriction/Modifying Enzymes Restriction Enzymes.
- Turns with an electric drill! Piston Fly Cutters for valve clearances that have changeable rods for different guide sizes. They are high speed steel cutters made in sizes ranging from 1” to 2-1/2” diameters.
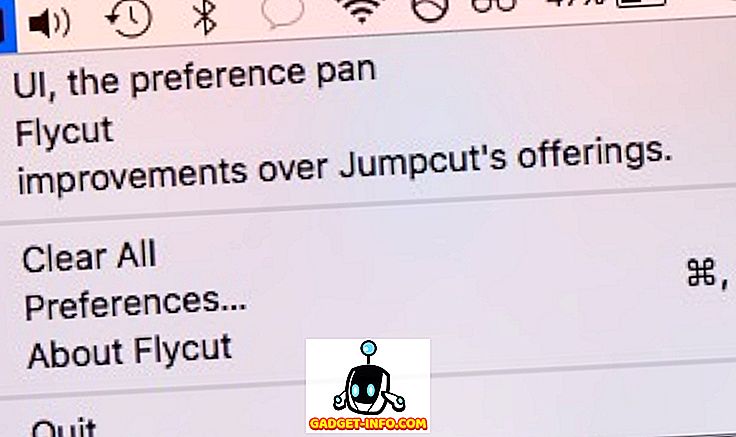
The physics are the same for the cutter, whether it’s a manual machine or a CNC machine.
I’m tempted to respond as one famous Starship Chief Engineer did with, “I canna change the laws of physics, Captain!” But, that’s just telling us we need to think about the problem differently: we don’t have to change the laws of physics, we just have to apply them properly.
Take the issue of trying to madly crank the handwheel to hit 100 inches per minute or some other similarly silly thing that G-Wizard may recommend to the manual machinist. First question is, “Why did it recommend that?” And the answer is, unless you keep chip load up, you run the risk of rubbing the cutter.
Consider this diagram:
Cutter at the top has large chip load relative to radius of cutting edge, so it cleanly slices off chips. Cutter at the bottom has a large cutting edge radius relative to the chip load. It can hardly get under the chip to slice, so it plows, scrapes, and rubs. It may produce a fine finish, but it does so by burnishing. This creates a lot of heat and is very hard on your cutting tools. When G-Wizard asks for a particular feedrate, and it seems too fast, it’s only because it’s trying to get the picture at the top where the cutter slices cleanly.
Okay, so how do we manage feedrate on machines that can’t feed fast enough? Here are some thoughts:
Be sure you tell G-Wizard what your maximum feedrate is–it will limit itself automatically. Let’s try an example. Take a 1/2″ TiAlN 3 flute in 6061, 1/2″ depth of cut, 1/8″ width of cut. Let’s say our spindle will do a maximum of 5500 rpm. We get back a feedrate of 78 IPM and a chip load of 0.0041″. If the spindle would do 10,000 rpm, it jumps up to 142 IPM to maintain the same chip load.
Now let’s say a manual machinist decides they can turn a handwheel twice a second and still be smooth, but that’s the limit on hand cranking. If each turn moves the table 0.100″, we’re moving at 2 * 60 * 0.1 = 12 inches per minute. That’s well short of our goal. If we override G-Wizard’s feedrate on the 5500 rpm spindle to be 12 IPM, we have a chip load of 0.0007″. I try not to let chip load fall below 0.001″ on carbide and maybe 0.0005″ on HSS if I am overriding G-Wizard. Those are just estimates of how low I can go and not get into that edge radius rubbing issue. So this cut is iffy for me.
How can G-Wizard help?
Well, let’s go to the Setup page and create a machine profile better suited to our manual machine:
Here’s a Machine Profile suited to a Manual Mill…
I just went in and customized some of the fields to be better suited to a manual mill. I didn’t bother with a lot of it–a manual mill has no toolchanger and we don’t care how fast it accelerates the spindle or which CNC Controller it uses (LOL), those are fields used by the G-Wizard Editor / Simulator. Here are the important points:
– Manual mills usually have a slower spindle rpm, so be sure to set that up. I used 5500 rpm.
– They have lower horsepower and use a spindle taper like R8
– No TSC (through spindle coolant), PCN (programmable coolant nozzle), and if they have flood, it is not strong and might as well be mist.
– Perhaps most important: set the feedrate based on how fast you can crank or how fast your power feed will allow! I used 12 IPM, which is 2 turns a second on a handwheel where 10 turns is an inch.
If we go back to the Feeds and Speeds calculator with that profile, we’ll see that G-Wizard has adjusted to the machine’s capabilities. Our 5500 rpm / 78 IPM cut is now a 3800 rpm / 12 IPM cut. That’s manageable! And, you’ll note the chip load will be 0.0011″. What G-Wizard has done is to try to balance all the factors and get the required feedrate down by slowing the spindle (good for tool life too!) and allowing the recommended 0.004″ chip load to fall as low as 0.0011″.
Fly Cutter Feeds and Speeds
Fly cutters on a manual mill…
Let’s talk Fly Cutter Feeds and Speeds as long as we’re talking G-Wizard for manual machinists. I get asked about Fly Cutters a lot, there is a lot of traffic to my site on those keywords, and Fly Cutters are very commonly used by manual machinists. In fact, I’ve created a dedicated page with a lot of information on fly cutters. While the CNC crowd will more often prefer facemills, even many CNC machinists realize that the very best surface finish often comes from fly cutting. Remove all but one insert from your facemill, and finish improves. The exception are those most expensive facemills where you can individually adjust the cutting height of each insert to 0.0001″, because that’s what it takes, and that’s why fly cutters can leave a better finish. Many say their secret weapon for fine aluminum finishing is a fly cutter with a PCD (diamond) insert. To learn more about the non-feeds and speeds aspects of fly cutters, please visit our Fly Cutters page. Now let’s get back to feeds and speeds:
How do we set up G-Wizard for a fly cutter?
The writer that prompted me to write this post had the right idea–just tell G-Wizard you’ve got a Facemill with only 1 insert. That’s exactly right. If your fly cutter has a lead angle, the ones pictured both do–the edge is angled, try using the lead angle feature on the Facemill type. If I do all that on G-Wizard, the result is: 1834 rpm @ 12 ipm for a 0.100″ DOC and 1.8″ cut width. That’s not too bad for hogging a surface flat, it’s a half horsepower cut, but there’s way too much chip load for a fine finish. It’s showing 0.0065″ chip load. That’s because it thinks you’ve got a nice facemill with some chunky carbide inserts that can take it. Surface speed is 1440 IPM.
A good manual machinist who wants a great finish on aluminum will grind themselves a razor sharp HSS tool and stick that into the fly cutter. It’ll look something like this:
Note the large radius, sharp edge, and steep positive rake on this HSS Fly Cutter tool…
A tool like that will put a beautiful finish on aluminum, but its edge is too delicate for tougher materials or for the carbide feeds and speeds G-Wizard wants to dish up. Let’s adjust for that with the following steps:
1. Bring up an HSS endmill and check out the chip load and surface speed. Chose something about the same scale as the flycutter’s tool. A 1/2″ endmill is fine. I see 400 SFM and maybe 0.003″ chip load.
2. Go back to your Facemill feeds and speeds and try using those figures for SFM and chip load.
3. If finishing, take the chip load down to 0.001″, or even less if you have a razor edge on that tool. The one pictured is knife sharp and I’d be comfortable as low as 0.0006″ or 0.0005″.
With those settings, G-Wizard gives 500 rpm @ 0.36 IPM. To convert that to seconds per handwheel rotation, multiply by 50 and we get one handwheel turn every 18 seconds. That will produce a fine finish indeed with such a cutter.
The 50 is just a rule of thumb that’s close, but a little fast. The real number is 16.67 seconds a turn, but its easier to remember 50. In fact, you can use the field arithmetic in G-Wizard to do the calculation. Just go to the feedrate and type “*50” and you’ll be looking at the number.
More Thoughts on Fly Cutters and Surface Finish
A fly cutter will often produce the best surface finish because they allow you to finish a very wide area in one pass with no overlap marks and the cut has a constant depth. If your face mill has individually adjustable insert heights, you probably won’t see a lot of benefit in a flycutter, but if not, you can easily convert a facemill to a flycutter by removing all but one insert, and it is interesting to experiment with the results. Reducing the number of inserts will necessitate a reduction in feedrate, but it may be worth it in terms of improved surface finish.
Some people swear that the best finish for aluminum is a flycutter large enough to cut your material in a single pass equipped with a PCD insert of the largest possible radius.
Like most mill cutters, your fly cutter will perform better with positive rake on the cutting tool. I haven’t yet seen any positive rake brazed carbide tools (which seem like the most common thing people stick in their flycutters), so I suppose you would either need an insert like a CCMT or you’d need to grind your own tool from HSS with some positive rake.
Fly cutters are very sensitive to tram. If you think about it, the cutter is apt to cut a concave instead of flat cut if your mill’s head is not trammed properly. Watch your workpiece carefully as the leading edge moves through the center of the fly cutter. All the cutting should have been done as it was travelling the first half of the way if you head is in tram (think about it carefull, that’s one geometry for one direction, so you actually have to see this behavior cutting in both directions to be sure). If it cuts more on the second half, you can be sure the tram is such that the head has that half tilted downward slightly. Also, the larger the fly cutter diameter, the more the tram effect is exaggerated.
In some cases, you may prefer the surface finish from a face mill or fly cutter on a mill that is slightly out of tram so it only cuts on one side.
I hope this gives a good idea of how manual machinists can use G-Wizard to good effect.
Like what you read on CNCCookbook?
Join 100,000+ CNC'ers! Get our latest blog posts delivered straight to your email inbox once a week for free. Plus, we’ll give you access to some great CNC reference materials including:
- Our Big List of over 200 CNC Tips and Techniques
- Our Free GCode Programming Basics Course
- And more!
Just enter your name and email address below:
100% Privacy: We will never Spam you!More articles you may like:
I got an email from a customer the other day who wondered if there wasn’t some way to make G-Wizard more focused to the needs of manual machinists. He felt that it was overly “CNC specific”, and wanted some sort of “CNC versus Manual” switch to make it easier. I need to cogitate more on the idea of a switch, but it is certainly true that if you start dialing up modern tooling in G-Wizard and cutting softer materials, you will end up with feeds and speeds that are impossible–the manual machinist just can’t crank the handwheel fast enough.
Let’s back up just for a second and realize a key thing:
The physics are the same for the cutter, whether it’s a manual machine or a CNC machine.
I’m tempted to respond as one famous Starship Chief Engineer did with, “I canna change the laws of physics, Captain!” But, that’s just telling us we need to think about the problem differently: we don’t have to change the laws of physics, we just have to apply them properly.
Take the issue of trying to madly crank the handwheel to hit 100 inches per minute or some other similarly silly thing that G-Wizard may recommend to the manual machinist. First question is, “Why did it recommend that?” And the answer is, unless you keep chip load up, you run the risk of rubbing the cutter.
Consider this diagram:
Cutter at the top has large chip load relative to radius of cutting edge, so it cleanly slices off chips. Cutter at the bottom has a large cutting edge radius relative to the chip load. It can hardly get under the chip to slice, so it plows, scrapes, and rubs. It may produce a fine finish, but it does so by burnishing. This creates a lot of heat and is very hard on your cutting tools. When G-Wizard asks for a particular feedrate, and it seems too fast, it’s only because it’s trying to get the picture at the top where the cutter slices cleanly.
Okay, so how do we manage feedrate on machines that can’t feed fast enough? Here are some thoughts:
Be sure you tell G-Wizard what your maximum feedrate is–it will limit itself automatically. Let’s try an example. Take a 1/2″ TiAlN 3 flute in 6061, 1/2″ depth of cut, 1/8″ width of cut. Let’s say our spindle will do a maximum of 5500 rpm. We get back a feedrate of 78 IPM and a chip load of 0.0041″. If the spindle would do 10,000 rpm, it jumps up to 142 IPM to maintain the same chip load.
Now let’s say a manual machinist decides they can turn a handwheel twice a second and still be smooth, but that’s the limit on hand cranking. If each turn moves the table 0.100″, we’re moving at 2 * 60 * 0.1 = 12 inches per minute. That’s well short of our goal. If we override G-Wizard’s feedrate on the 5500 rpm spindle to be 12 IPM, we have a chip load of 0.0007″. I try not to let chip load fall below 0.001″ on carbide and maybe 0.0005″ on HSS if I am overriding G-Wizard. Those are just estimates of how low I can go and not get into that edge radius rubbing issue. So this cut is iffy for me.
How can G-Wizard help?
Well, let’s go to the Setup page and create a machine profile better suited to our manual machine:
Here’s a Machine Profile suited to a Manual Mill…
I just went in and customized some of the fields to be better suited to a manual mill. I didn’t bother with a lot of it–a manual mill has no toolchanger and we don’t care how fast it accelerates the spindle or which CNC Controller it uses (LOL), those are fields used by the G-Wizard Editor / Simulator. Here are the important points:
– Manual mills usually have a slower spindle rpm, so be sure to set that up. I used 5500 rpm.
– They have lower horsepower and use a spindle taper like R8
– No TSC (through spindle coolant), PCN (programmable coolant nozzle), and if they have flood, it is not strong and might as well be mist.
– Perhaps most important: set the feedrate based on how fast you can crank or how fast your power feed will allow! I used 12 IPM, which is 2 turns a second on a handwheel where 10 turns is an inch.
If we go back to the Feeds and Speeds calculator with that profile, we’ll see that G-Wizard has adjusted to the machine’s capabilities. Our 5500 rpm / 78 IPM cut is now a 3800 rpm / 12 IPM cut. That’s manageable! And, you’ll note the chip load will be 0.0011″. What G-Wizard has done is to try to balance all the factors and get the required feedrate down by slowing the spindle (good for tool life too!) and allowing the recommended 0.004″ chip load to fall as low as 0.0011″.
Fly Cutter Feeds and Speeds
Fly cutters on a manual mill…
Let’s talk Fly Cutter Feeds and Speeds as long as we’re talking G-Wizard for manual machinists. I get asked about Fly Cutters a lot, there is a lot of traffic to my site on those keywords, and Fly Cutters are very commonly used by manual machinists. In fact, I’ve created a dedicated page with a lot of information on fly cutters. While the CNC crowd will more often prefer facemills, even many CNC machinists realize that the very best surface finish often comes from fly cutting. Remove all but one insert from your facemill, and finish improves. The exception are those most expensive facemills where you can individually adjust the cutting height of each insert to 0.0001″, because that’s what it takes, and that’s why fly cutters can leave a better finish. Many say their secret weapon for fine aluminum finishing is a fly cutter with a PCD (diamond) insert. To learn more about the non-feeds and speeds aspects of fly cutters, please visit our Fly Cutters page. Now let’s get back to feeds and speeds:
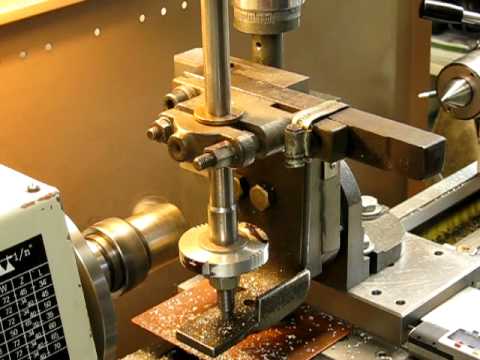
How do we set up G-Wizard for a fly cutter?
The writer that prompted me to write this post had the right idea–just tell G-Wizard you’ve got a Facemill with only 1 insert. That’s exactly right. If your fly cutter has a lead angle, the ones pictured both do–the edge is angled, try using the lead angle feature on the Facemill type. If I do all that on G-Wizard, the result is: 1834 rpm @ 12 ipm for a 0.100″ DOC and 1.8″ cut width. That’s not too bad for hogging a surface flat, it’s a half horsepower cut, but there’s way too much chip load for a fine finish. It’s showing 0.0065″ chip load. That’s because it thinks you’ve got a nice facemill with some chunky carbide inserts that can take it. Surface speed is 1440 IPM.
A good manual machinist who wants a great finish on aluminum will grind themselves a razor sharp HSS tool and stick that into the fly cutter. It’ll look something like this:
Note the large radius, sharp edge, and steep positive rake on this HSS Fly Cutter tool…
A tool like that will put a beautiful finish on aluminum, but its edge is too delicate for tougher materials or for the carbide feeds and speeds G-Wizard wants to dish up. Let’s adjust for that with the following steps:
1. Bring up an HSS endmill and check out the chip load and surface speed. Chose something about the same scale as the flycutter’s tool. A 1/2″ endmill is fine. I see 400 SFM and maybe 0.003″ chip load.
2. Go back to your Facemill feeds and speeds and try using those figures for SFM and chip load.
3. If finishing, take the chip load down to 0.001″, or even less if you have a razor edge on that tool. The one pictured is knife sharp and I’d be comfortable as low as 0.0006″ or 0.0005″.
With those settings, G-Wizard gives 500 rpm @ 0.36 IPM. To convert that to seconds per handwheel rotation, multiply by 50 and we get one handwheel turn every 18 seconds. That will produce a fine finish indeed with such a cutter.
The 50 is just a rule of thumb that’s close, but a little fast. The real number is 16.67 seconds a turn, but its easier to remember 50. In fact, you can use the field arithmetic in G-Wizard to do the calculation. Just go to the feedrate and type “*50” and you’ll be looking at the number.
More Thoughts on Fly Cutters and Surface Finish

A fly cutter will often produce the best surface finish because they allow you to finish a very wide area in one pass with no overlap marks and the cut has a constant depth. If your face mill has individually adjustable insert heights, you probably won’t see a lot of benefit in a flycutter, but if not, you can easily convert a facemill to a flycutter by removing all but one insert, and it is interesting to experiment with the results. Reducing the number of inserts will necessitate a reduction in feedrate, but it may be worth it in terms of improved surface finish.
Some people swear that the best finish for aluminum is a flycutter large enough to cut your material in a single pass equipped with a PCD insert of the largest possible radius.
Like most mill cutters, your fly cutter will perform better with positive rake on the cutting tool. I haven’t yet seen any positive rake brazed carbide tools (which seem like the most common thing people stick in their flycutters), so I suppose you would either need an insert like a CCMT or you’d need to grind your own tool from HSS with some positive rake.
Fly cutters are very sensitive to tram. If you think about it, the cutter is apt to cut a concave instead of flat cut if your mill’s head is not trammed properly. Watch your workpiece carefully as the leading edge moves through the center of the fly cutter. All the cutting should have been done as it was travelling the first half of the way if you head is in tram (think about it carefull, that’s one geometry for one direction, so you actually have to see this behavior cutting in both directions to be sure). If it cuts more on the second half, you can be sure the tram is such that the head has that half tilted downward slightly. Also, the larger the fly cutter diameter, the more the tram effect is exaggerated.
In some cases, you may prefer the surface finish from a face mill or fly cutter on a mill that is slightly out of tram so it only cuts on one side.
I hope this gives a good idea of how manual machinists can use G-Wizard to good effect.
Like what you read on CNCCookbook?
Join 100,000+ CNC'ers! Get our latest blog posts delivered straight to your email inbox once a week for free. Plus, we’ll give you access to some great CNC reference materials including:
- Our Big List of over 200 CNC Tips and Techniques
- Our Free GCode Programming Basics Course
- And more!
Flycut Windows
Just enter your name and email address below:
100% Privacy: We will never Spam you!Gpi Flycut Tool
Flycut Github
More articles you may like:
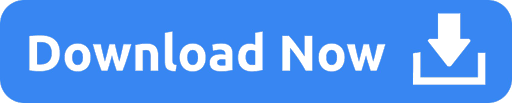